-
AlignOps| Dec 23, 2024
What is a Pick Ticket? A Guide to Warehouse Efficiency
Time is money, especially in a warehouse. The time it takes to locate an ordered product directly impacts the bottom line. A pick ticket can help or hinder the speed of pick and pack operations.
What is a Pick Ticket?
Pick tickets in a warehouse setting are instructions for staff to locate and gather specific products for shipment, restocking, or transfer to another location. Typically, a pick ticket will include critical details such as:
- Product identification: SKU numbers, item names, or barcodes.
- Quantity to pick: The amount of each item required for the order.
- Location information: The specific location or bin within the warehouse where the item is stored.
- Order details: Customer order, shipment, or transfer information.
The purpose of the pick ticket is to streamline picking and reduce errors. A pick ticket management system maintains the efficiency of the entire warehouse operation. It ensures that the right products are gathered in the right quantities at the right time to meet customer demand or internal inventory needs.
Pick Ticket vs Packing Slip
While both a pick ticket and a packing slip are essential documents in warehouse and logistics operations, they serve different purposes. The pick ticket is a picking tool, while the packing slip is a shipping tool:
- Pick ticket: The pick ticket guides the warehouse staff in locating and selecting items from inventory to fulfill orders. Once they have selected the items to fulfill the order, the process moves to packing.
- Packing slip: The packing slip occurs after the picking process. It is used during packing and shipping to verify that all the items listed on the order are included. The packing slip may contain additional shipping and billing information but does not play a role in the picking phase.
Warehouse Picking Efficiency and the Role of Pick Tickets
Efficiency is the most critical part of warehouse operations, particularly in picking. A slow or error-prone picking system can delay or miss orders and, as you can imagine, reduce customer satisfaction.
Here's how pick tickets contribute to improving warehouse picking efficiency:
- Streamlined processes: Pick tickets provide clear, specific instructions on what to pick and where to find it. When implemented properly, they reduce ambiguity and confusion, which helps warehouse staff work faster and more accurately.
- Reduced errors: A well-designed pick ticket includes details like the exact product location, minimizing the chances of picking the wrong item or quantity. It reduces the need for re-picking, which can be time-consuming and costly.
- Better inventory management: With detailed tracking on each pick ticket, warehouse managers gain real-time visibility into inventory levels. They can also track item movements between locations and maintain a more organized warehouse overall.
- Faster fulfillment: An efficient pick ticket management system can guide pickers directly to the ordered items. Ultimately, it takes less time to locate inventory, which speeds up order fulfillment.
The Pick Ticket Management System: ToolWatch by AlignOps
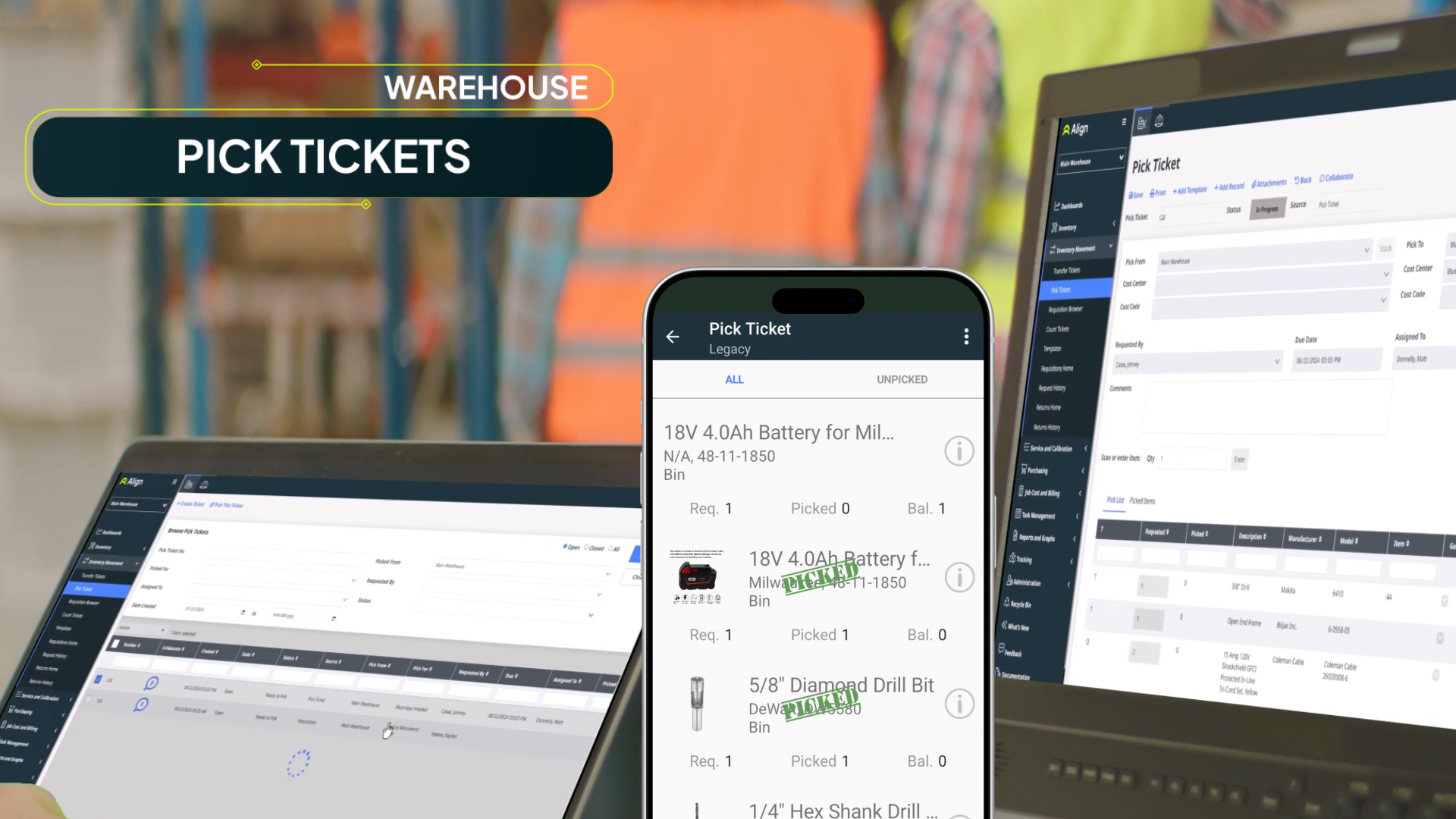
While pick tickets are essential in any warehouse operation, managing them requires a sophisticated system. This process is the sweet spot where the ToolWatch by AlignOps Pick Ticket and Transfers Management Software can make all the difference. This platform offers an integrated solution that simplifies the management of tools, equipment, and consumables across job sites and warehouses.
The ToolWatch by AlignOps pick ticket and transfer functionality allows warehouse teams to move inventory while providing visibility and efficient real-time tracking.
Here are the key features of ToolWatch by AlignOps' pick ticket software:
- Real-time tracking: ToolWatch by AlignOps provides real-time assets and inventory tracking. When a field worker picks an item, they can instantly update its location using the AlignOps Field App on their smartphone or tablet. The updated information is immediately available to all team members.
- Seamless asset movement: ToolWatch by AlignOps software allows tracking of tools, equipment, and materials. Whether moving assets from a warehouse to a job site or from one project to another, AlignOps ensures every transfer is documented and visible across the organization.
- Cost tracking: ToolWatch by AlignOps software automatically stops job cost and billing calculations when the item moves. Simultaneously, charges start accruing on the new project. Automation makes it easier to maintain accurate cost tracking and keeps your financial data current.
- Mobile-friendly: ToolWatch by AlignOps’ mobile app, compatible with Android and iOS, ensures warehouse and field teams can update pick ticket information on the go. With just a few taps, field workers can indicate that an item has been picked and moved, making the entire process faster and more efficient.
- Enterprise-wide visibility: With ToolWatch by AlignOps, you can maintain enterprise-wide visibility into the location of all your tools and equipment, whether they’re in the warehouse or on a job site. This holistic view of asset movement ensures your inventory is always accounted for and accessible.
The Bottom Line
Pick tickets can make your warehouse more efficient by streamlining picking, reducing human errors, and improving inventory management. ToolWatch by AlignOps takes this process further by providing a powerful pick ticket management system that enhances asset tracking, visibility, and cost management across an entire organization.
For businesses looking to optimize warehouse operations, AlignOps' pick ticket and transfer solutions offer a comprehensive approach to managing inventory movement.
To learn more about how ToolWatch by AlignOps can improve your warehouse picking and asset management processes, book a demo to see these tools in action.
Q: How can I improve picking accuracy in my warehouse?
To improve warehouse picking accuracy, consider implementing barcode scanning or RFID technology to reduce human error. Train your staff regularly on the importance of accuracy and familiarize them with the location of high-demand items. Another strategy is to organize the warehouse for optimal flow, grouping frequently picked items closer to the packing and shipping areas. Additionally, a pick-to-light system or voice-picking technology can help guide pickers to the correct items more efficiently, ensuring higher accuracy while speeding up the process.
Q: What is wave picking, and how does it improve warehouse efficiency?
Wave picking is a strategy grouping multiple orders into waves, allowing workers to pick items for several orders simultaneously. Instead of picking individual orders sequentially, wave picking organizes the picking process by specific time frames or zones, optimizing picking routes and minimizing downtime. It’s an approach that improves efficiency by maximizing labor and reducing travel time within the warehouse. For high-volume warehouses, wave picking helps synchronize the picking process with other operations, such as packing and shipping, resulting in faster order fulfillment and more efficient resource allocation.
About AlignOps
At AlignOps, we make construction safe, productive, and profitable. As the construction industry's first and most comprehensive operations management platform, AlignOps’ suite of powerful tools delivers operational visibility and control that drives results. Formed in 2024, AlignOps is powered by four innovative market leaders: ToolWatch construction management software, Safety Reports mobile safety and compliance, FleetWatcher construction fleet management software, and busybusy time tracking.